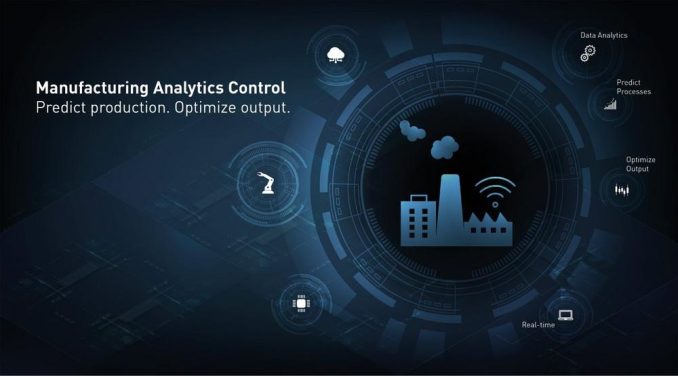
Die Produktfamilie „Manufacturing Analytics Control” zielt auf die Analyse und Optimierung der Fertigungsleistung ab und trifft Vorhersagen über die zukünftige Prozessqualität. Sie kann ergänzend zum Manufacturing-Operations-Management-System iTAC.MOM.Suite eingesetzt werden, das auf die Planung, Steuerung und Überwachung von Produktionsprozessen in Echtzeit ausgelegt ist, wird jedoch auch als Stand-Alone-Lösung implementiert.
„Manufacturing Analytics Control“ vereint Software-Produkte von iTAC und der Tochtergesellschaft Cogiscan zu einem Portfolio. Ein zentraler Baustein ist die Streaming-Engine, die Daten aus mehreren Quellen in Echtzeit verarbeiten und verknüpfen kann. Auf dieser Basis kann die Leistung der gesamten Fertigungsumgebung analysiert werden. „Wir ebnen den Weg für ein umfassendes Performance-Verständnis. Dies unterstützt die operative Planung, ermöglicht die Identifizierung von Verbesserungspotenzialen und trägt letztlich zu einer effizienteren und rentableren Produktion bei“, erklärt Martin Heinz, Vorstandsmitglied bei iTAC.
Die Lösung bietet umfassende Möglichkeiten der Data Analytics, sowohl in Echtzeit als auch anhand historischer Daten. Damit ergibt sich ein klarer Einblick in die aktuelle und vergangene Leistung, insbesondere bei kritischen Maschinen und Prozessen. Mit vordefinierten Key Performance Indicators (KPIs) können Unternehmen Leistungsparameter genau überwachen und bewerten. Zudem können die Prozessverantwortlichen die Abweichungen vom Soll-Zustand schnell erkennen und effizient darauf reagieren. Das trägt dazu bei, die Produktionsstörungen zu minimieren und die Betriebsleistung zu optimieren.
Die Möglichkeit, Dashboards individuell anzupassen, erlaubt es Unternehmen, die relevanten KPIs und Daten nach ihren spezifischen Anforderungen und Prioritäten zu visualisieren – die Basis für eine maßgeschneiderte Analyse und Entscheidungsfindung. Dabei lassen sich Widgets aus verschiedenen Produkten in einem Dashboard beliebig kombinieren. Durch einfaches Drag-and-Drop können Widgets beispielsweise für die Analyse von Öfen, Nozzles oder Feedern ausgewählt und flexibel platziert werden. Ein weiteres Alleinstellungsmerkmal ist, dass Maschinendaten der vor- und nachgelagerten Prozesse direkt miteinander verglichen werden können, um z.B. eine Analyse in Echtzeit durchzuführen. Dabei werden die Messdaten mittels KI mit den Daten der AOIs (Automatisch optische Inspektion) und SPIs (Solder Paste Inspection) korreliert und in einer Heatmap abgebildet.
Einfache Implementierung und Entlastung auf mehreren Ebenen
„Manufacturing Analytics Control“ bietet verschiedene Vorteile, um Mehrwert aus Daten zu schöpfen, und ist direkt einsetzbar. Es handelt sich um ein Add-on für Unternehmen mit vorhandener Infrastruktur. Die Implementierung und Anwendung sind denkbar einfach: Für den Start werden keine Data Scientists benötigt und es ist keinerlei Programmiererfahrung notwendig.
Die Lösung bietet „out of the box“ standardmäßig einsatzbereite Use Cases, die speziell auf die Anforderungen oder Bedürfnisse verschiedener Branchen zugeschnitten sind. Dabei ist Konnektivität gewährleistet, so dass sich schnelle und unkomplizierte Verbindungen zu Maschinen aufbauen lassen. Es ist kein spezialisiertes Connectivity-Engineering-Team erforderlich.
Das Datenmodell wurde bereits in verschiedenen Industriezweigen erfolgreich getestet. Es beinhaltet umfassende Datenprüfungen, Fehlerprüfungen, Interpretationen und standardisierte Auswertungen. Diese Funktionalitäten dienen nicht nur der Qualitätssicherung, sondern auch der Entlastung des Reporting-Teams und der Datenerfasser.
Die Lösung vereinfacht die Aufgaben des Data Engineers und macht Maschinendaten interpretierbar, indem sie Daten von einer Maschine mit notwendigen Kontextinformationen kombiniert, sodass unstrukturierte Daten zu strukturierten Daten werden. Weiterhin werden diese Daten in umsetzbare Workflows verwandelt. Die Workflow-Schnittstellen wie MS Teams ermöglichen die Echtzeit-Kontrolle von Aktionen, Daten und Maschinen. Außerdem ist der Weg frei für geschlossene Regelkreise und proaktives Problemmanagement. Weiterer Mehrwert aus den Daten lässt sich mittels KI schaffen, denn das Hinzufügen von AI/ML zu den Arbeitsabläufen ist einfach möglich.
Die iTAC Software AG, ein eigenständiges Unternehmen des Maschinen- und Anlagenbaukonzerns Dürr, bietet internetfähige Informations- und Kommunikationstechnologien für die produzierende Industrie. Das 1998 gegründete Unternehmen zählt heute zu den führenden MES/MOM-Herstellern. Die iTAC.MOM.Suite ist ein ganzheitliches Fertigungsmanagementsystem, das weltweit bei Unternehmen unterschiedlicher Industriezweige wie Automotive, Elektronik/EMS, Telekommunikation, Medizintechnik, Metallindustrie und Energie zum Einsatz kommt. Weitere Systeme und Lösungen zur Umsetzung der IIoT- und Industrie 4.0-Anforderungen runden das Portfolio ab. Die iTAC Software AG hat ihren Hauptsitz in Montabaur in Deutschland sowie eine Niederlassung in den USA, in Mexiko, China und Japan, und verfügt über ein weltweites Partnernetzwerk für Vertrieb und Service. Die Philosophie von iTAC ist es, Menschen, Daten und Systeme miteinander zu verbinden.
Der Dürr-Konzern ist ein weltweit führender Maschinen- und Anlagenbauer mit ausgeprägter Kompetenz in den Bereichen Automatisierung, Digitalisierung und Energieeffizienz. Seine Produkte, Systeme und Services ermöglichen hocheffiziente und nachhaltige Fertigungsprozesse in unterschiedlichen Industrien. Der Dürr-Konzern beliefert vor allem die Automobilindustrie, Produzenten von Möbeln und Holzhäusern sowie die Branchen Chemie, Pharma, Medizinprodukte und Elektro. Im Jahr 2022 erzielte er einen Umsatz von 4,3 Mrd. €. Das Unternehmen hat rund 19.000 Beschäftigte und verfügt über 123 Standorte in 32 Ländern. Der Dürr-Konzern agiert mit den drei Marken Dürr, Schenck und HOMAG sowie mit fünf Divisions am Markt.
iTAC Software AG
Aubachstraße 24
56410 Montabaur
Telefon: +49 (2602) 1065-0
Telefax: +49 (2602) 1065-30
https://www.itacsoftware.com
Inbound Marketing
Telefon: +49 2602 106520
E-Mail: alina.leber@itacsoftware.com
Geschäftsführerin
Telefon: +49 (211) 9717977-0
E-Mail: pr@punctum-pr.de