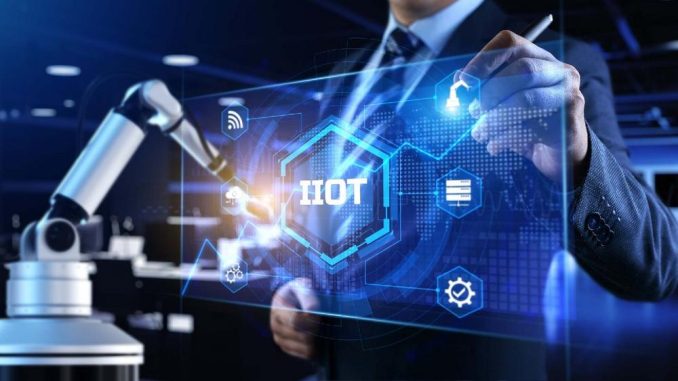
Zur Begriffsklärung: IoP, IoT und IIoT
Bis Ende der 90iger Jahre nutzte man das Internet hauptsächlich, um Informationen zu erlangen. Mit dem World Wide Web änderte sich dies. Jedem stand auf einmal eine fast unbegrenzte Infrastruktur zur Verfügung, um miteinander zu kommunizieren, oder sich gegenseitig zu informieren. Während 1991 nur ca. 500.000 Rechner angeschlossen waren, stieg dieser Wert innerhalb von nur vier Jahren auf 10 Millionen, hat sich innerhalb der nächsten fünf Jahre ver-zweiunddreißig-facht und betrug im Jahr 2009 bereits 1,6 Milliarden. Es war dann die mobile Nutzung des Internets, die, so beschreibt es die Studie „Digitaler Wandel in Familienunternehmen. Das Handbuch“, (A. Weissmann; S. Wegerer, 2018) „einen Quantensprung in der Nutzung“ verursachte. Heute gibt es nahezu niemanden, der nicht in irgendeiner Weise Zugang zum Internet hat und beinahe nichts, was sich nicht zumindest vernetzen ließe. Man unterscheidet zwischen der Vernetzung von Menschen, dem Internet of People (IoP), dem Vernetzen von Maschinen, untereinander und mit Rechenzentren, dem Internet of Things (IoT), sowie dem Vernetzen von Maschinen, Menschen und Systemen, worunter auch das IIoT fällt.
Das Internet of Things: IoT
Was sich im ersten Moment anhört wie eine Vision aus einem Science-Fiktion Roman, ist bereits Teil unserer Realität, – man denke an dieser Stelle einfach nur an Smart Watches, die die Vitalfunktionen eines Menschen aufzeichnen und ihm Informationen über sich selbst und Lebensgewohnheiten wie etwa Schlafrhythmus oder Bewegungsabläufe, nicht nur zur Verfügung stellen -, sondern zudem auswerten und individuell beurteilen können. Die Maschine wird genau deswegen als „Smart Product“ bezeichnet, weil sie Daten während der Fertigungs- und Nutzungsphase sammeln und kommunizieren kann. Daraus hat sich mittlerweile so einiges entwickelt. Für „Urban Explorer“, so die Bezeichnung für ein Tech-interessiertes Publikum, wurden per App beheizbare Jacken und Westen kreiert. Yoga-Fans können heute Sportkleidung tragen, die sie per Vibration am entsprechenden Körperteil darauf hinweist, dass eine Pose nicht ordentlich ausgeführt wird. Die Liste vernetzter Objekte ist endlos und reicht von Thermostaten, Musikanlagen, Autos oder Haustüren, die mit dem Smartphone verbunden werden können, bis über Android Datenbrillen oder Smart Sneakern, hin zu Vielem mehr. Ganze Bereiche wie Wohnen, Fahren oder auch Sport sind davon durchdrungen. Das IoT Konzept ist als solches verbraucherorientiert, so stellt auch das Whitepaper „Industrial Internet of Things: Referenzarchitektur für die Kommunikation.“ des Fraunhofer Instituts für eingebettete Systeme und Kommunikationstechnik fest. Darüber hinaus treibt es aber die reale und die virtuelle Welt dazu an, sich auch zu einem industriellen Internet der Dinge zu verbinden.
Das Industrial Internet of Things: IIoT und der Status Quo
Dieses repräsentiert, im Gegensatz zum verbraucherorientierten Umfeld des IoT, dessen produzierendes, industrielles Umfeld. Es bezeichnet damit eher ein strategisches Konzept als reine Technologie. Zu den im IIoT angewandten Technologien zählen: Mobile und kabelgebundene Vernetzung, Big Data, Cyber-physische Systeme (CPS), Cloud Computing, Edge Computing, Künstliche Intelligenz (KI) und Maschinelles Lernen (ML). Auf dem Weg zur Industrie 4.0 begleitet es deswegen auch alle Familienunternehmen, wenn auch noch in unterschiedlich starker Ausprägung: Laut der „Neue(n) Studie zu Industrial IoT: Deutsche Industrieunternehmen haben Potenzial verschlafen“, (International Data Cooperation, 2022) hinken deutsche Unternehmen insgesamt bei der Einführung und optimalen Nutzung von IIoT im internationalen Vergleich hinterher. Bei einer Befragung von 250 industriellen oder industrienahen Unternehmen, Anfang des Jahres 2022, stellte sich heraus, dass nur 29 % aktiv IIoT-Projekte umsetzen. Nur ein Drittel davon misst den Erfolg dieser Projekte und nur ein Viertel hat Entscheidungsregeln entwickelt, um IIoT-Projekte gezielt zu steuern. Der IDC bedauert dies, da er im IIoT und damit einer datenzentrierten Unternehmenskultur den optimalen Werkzeugkasten sieht, um Unsicherheiten und kurzfristigen Veränderungen zu begegnen. Mit, durch IIoT ermöglichten, neuen datenbasierten Produkten, Services und Geschäftsmodellen könnte man auch den gegenwärtigen Herausforderungen der Wirtschaft effektiv etwas entgegensetzen. Der Blick auf Familienunternehmen zeigt jedenfalls eines: Die Bereitstellung solcher „Werkzeugkästen“ wird von einigen unter ihnen selbst geleistet und ist auch während eines laufenden Betriebes umsetzbar.
Ifm: Das IIoT als digitaler Werkzeugkasten
Einer der Anbieter ist ifm, ein weltweit agierender Vertreiber und Hersteller von Sensoren, Steuerungen, Software und Systemen für die industrielle Automatisierung sowie Pionier im Bereich der Industrie 4.0. ifm entwickelt und implementiert ganzheitliche Lösungen für die Digitalisierung. Mit „ifm moneo“ bietet das Unternehmen eine IIoT-PlattformSoftware, die modular aufgebaut ist. Das bedeutet, dass sie mit den Anforderungen der jeweiligen Kund:innen mitwächst und sukzessive, bedarfsorientiert erweitert werden kann. moneo findet seinen Einsatz, um Prozesse und Daten zu visualisieren, zur Sicherung und Steigerung von Qualität für Produkte, Maschinen und Anlagen. Neben der Organisation von Wartung und Instandhaltung, können auch Effizienz- und Energie-Betrachtungen mit der Software durchgeführt werden. Die Parametrierung von IO-Link Sensoren und IO-Link Mastern, auch von Fremdherstellern ist eine zentrale Funktion innerhalb moneo. Die Basissoftware moneo OS, bietet flexibles Usermanagement, in dem unterschiedliche Berechtigungsstufen und Aufgaben, je User, bzw. Usergruppen verwaltet werden. Ein intuitives Device Management erleichtert die Anbindung neuer Devices, sowie auch, neue Anlagestrukturen abzubilden. Die generierte Transparenz aller Daten und Prozesse ermöglicht es die Potenziale voll auszuschöpfen, Energie- und Ressourceneinsparung aufzudecken und jeweils entsprechende Folgeaktivitäten und -prozesse anzustoßen. IIoT wird damit nicht nur intern, sondern auch extern zu einem effektiven Faktor. Es generiert Wettbewerbsvorteil und Wachstum bei gleichzeitig reduzierten Kosten.
Ein Blick in den Werkzeugkoffer: Intelligente Pumpenüberwachung
Ein konkretes Beispiel für eines der vielen standardisierten Funktionsmodule, die in den Software Solutions des Werkzeugkoffers von moneo enthalten sind, liefert die intelligente Pumpenüberwachung mittels des „moneo SmartLimitWatchers“. Insgesamt werden Pumpen eher selten überwacht. Das liegt zum Teil daran, dass sie aufgrund ihres Betriebs in verschiedenen Drehzahlbereichen statisch nur schwer zu überwachen sind. ifm moneo sammelt Daten zu folgenden kritischen Prozessgrößen: Durchfluss, Drehzahl, Druck, Temperatur und Schwingungsdaten. Über diese Daten wird dann ein Normalzustand definiert und modelliert, der es erlaubt, Abweichungen davon zu bemerken. Es ist maßgeblich, dass der „SmartLimitWatcher“ hierbei in der Lage ist, dynamische Grenzwerte zu setzen, die sich dem jeweiligen Betriebszustand und den deshalb unterschiedlichen Zulässigkeiten individuell anpassen. Die Messung des Durchflusses erfolgt beispielsweise anhand der Hilfsvariablen wie Drehzahl, Pumpendruck und Schwingungsdaten. Diese machen sein Verhalten abbildbar. Steigt der Durchfluss an, kann man das anhand steigender Drehzahl und steigendem Pumpendruck in Echtzeit ablesen und entsprechend reagieren.
Mehrwert: Qualitätssicherung und Vermeidung von Ausschuss
Die gesammelten Daten des Durchflusses selbst bieten wiederum zusätzlichen Benefit in der Analyse. Sie garantieren zum Beispiel die Reinigungsprozesse in der Lebensmittel- und Getränkeindustrie. Zum Einsatz kommen hier Sensoren, die sowohl die Leitfähigkeit als auch die Konzentration von unterschiedlichen Medien wie Reinigungsmitteln, Spülwasser und Lebensmitteln, genauer die Phasentrennung zwischen Spülwasser, Laugen- oder säurehaltigen CIP-Lösungen und dem Produkt, erkennen können. Diese genaue Messung des Prozesses gewährleistet nicht nur die Qualität und Sicherheit des Produktes, indem sie genau kontrollieren kann, dass alle Chemikalien aus den Leitungen komplett ausgespült sind. Sie verhindert auch einen Ausschuss an Produkt oder Spülwasser, indem sie die Reinigungszyklen optimiert und die Anlagenverfügbarkeit mittels durchgehender Produktverfolgung verbessert.
WAGO: Sine Qua Non! Daten als Grundelement jeder Wertschöpfung
Doch wie verbreitet ist die Sammlung und zielgerichtete Analyse von Daten bislang auch anderen Ortes? Wie die International Data Cooperation in oben genannter Studie[1] betont, liegt die wesentliche Voraussetzung für den Erfolg des IIoT und einer übergreifenden digitalen Transformation der Industrie, in einer definierten und ganzheitlichen Daten- und Analytics Strategie: „Erst wenn Daten aus der OT und dem Business in einer holistischen Plattform verlässlich aggregiert sind und je nach Anforderungen des IIoT-Anwendungsszenarios zur richtigen Zeit am richtigen Ort verarbeitet werden können, kann eine stimmige IIoT-Strategie definiert und erfolgreich umgesetzt werden“, so heißt es hier. Bemängelt wird die Tatsache, dass sich derzeit die Daten- und Analyseziele vielerorts noch an kurzfristigen Businesszielen ausrichten. Im Hinblick auf das Ziel einer ganzheitlichen Datenplattform kann dies höchstens als Basis zur Weiterentwicklung dienen. Zur Veranschaulichung dieser Einschätzung der Lage, bezieht sich WAGO, einer der weltweit führenden Anbieter elektrischer Verbindungs- und Automatisierungstechnik sowie der Interface Elektronik, auf seiner Internetseite auf die Studie „How to navigate Ditgitization of the manufactoring sector“ von McKinsey. Sie besagt, dass zum Beispiel auf deutschen Bohrinseln von allen Daten, die ca. 300.000 Sensoren bereitstellen, bislang nur 1 % genutzt und, auch im Automationsumfeld, meistens nur für Echtzeitanwendung und Fehlerdetektion verwendet werden. Dabei sind es Daten, über die, wie WAGO betont, heutzutage der Weg der Wertschöpfung, maßgeblich und unausweichlich führt. Während man bislang den Erfolg eines Unternehmens an die Faktoren Personal, Technologie und Kapital knüpfte, kommen heute Daten hinzu. In WAGOs White Paper, „Chancen der Digitalisierung und Modularisierung“ wird dies in einer Gegenüberstellung von „Heute“ versus „den Anfängen der Industrialisierung“ verdeutlicht:
Megatrend: Von Industrialisierung zur Individualisierung
Einst galt die goldene Regel: je mehr Stückzahlen man in die Produktion gibt, desto rentabler wird das Geschäft. Der Fokus lag dementsprechend immer auf einer Vereinheitlichung der Ware. Vielleicht genau dadurch angestoßen, schätzte es der Endkunde im Laufe der Zeit aber immer mehr, sein individualisiertes Produkt erstehen zu können, sei es hinsichtlich der Farbigkeit, der Form oder auch weitergehender, individueller Kombinationsmöglichkeiten. Egal ob beim Zusammenstellen der Ausstattung eines neuen Autos, oder der Vielfalt an Geschmacksrichtungen eines Produktes im Supermarktregal, lange war es die optimierte, automatisierte Massenfertigung, die die geschätzte Wahlmöglichkeit zu garantieren hatte.
Sonderanfertigung als Standard! Adieu Automatisierungspyramide.
Mit der Industrie 4.0 begegnet man den Erwartungen jedoch auf ganz grundsätzlich neue Weise. „Die Sonderanfertigung wird zum Standard, lautet die Logik“, so liest man hier. Das Kreieren des „eigenen Lieblings-Müslis“ ist heutzutage fast genauso geläufig wie das Konfigurieren und freie Gestalten des eigenen „costumized“ Sneakers. Notwendig wird damit eine, in den Fertigungsprozess integrierte, standardisierte, kostenoptimierte Einzelanfertigung, die ohne flexible und hochautomatisierte Anlagentechnik jedoch zunehmend unmöglich wird. Eine Produktion von Unikaten hat allerdings weitreichende Folgen und Anforderungen für und an alle Instanzen einer Lieferkette. Kürzere Produktzyklen oder individuelle Anfertigungen erfordern allerseits ein hohes Maß an Flexibilität sowie zunehmend auch an Vernetzung und Dezentrierung. Die klassische Automatisierungspyramide mit einer zentralen Steuerung an der Spitze dankt damit langsam ab.
Jetzt wird durchgestartet! Wie der erste Schritt gelingt.
Jürgen Pfeifer, IoT- und Cloud-Partnermanager bei WAGO, hat in einem Podcast zum Thema „Fabrik der Zukunft“ im Gespräch mit Tobias Herwig erklärt, wie man den Start in die Digitalisierung mittels der Vernetzung von Maschinen in einer Cloud, schrittweise gestalten kann. Aus seiner Perspektive ist die Lage lange nicht so düster, wie sie in den Medien oft gezeichnet wird. „Ich sehe, gerade auch in den aktuellen Kundengesprächen, dass das Thema an Fahrt gewinnt. Persönlich kann ich sagen: Es wird jetzt mehr denn je durchgestartet!“, so führt er aus. In seinen Augen besteht die größte Aufgabe oder Herausforderung darin, den Entscheider:innen die Angst zu nehmen und ihnen Mut zu machen, den Schritt in die Digitalisierung zu wagen. Als wesentlichen „Knackpunkt“ einer Entscheidung für den ersten Schritt identifiziert er das Thema der Anbindung eines Maschinenparks. Gerade bei älterer, heterogener Bestands-Hardware samt den jeweils verbauten unterschiedlichsten Steuerungen, kann sich dies herausfordernd gestalten. Es ist aber nie unüberwindbar, wie er betont. Grundsätzlich stellt sich zu Anfang immer die Frage, welche Daten man wofür im ersten Schritt nutzbar machen will, mithin, welche Maschinen vernetzt werden sollen. Ist man sich darüber im Klaren, lautet die nächste Frage, welche Protokolle jeweils gegeben sind. Wie steht es um die Konnektivität? Das Ergebnis entscheidet dann, ob man die Anbindung über die Steuerung selbst, oder über ein Signal, also einen Sensor angeht. Gerade bei älteren Maschinen ist oft unklar, wo relevante Daten in der Steuerung liegen, oder was sie bedeuten. Die Generierung eines Protokoll-Gateways für die Steuerung erweist sich in solchen Fällen als unwirtschaftlich. Jürgen Pfeiffer verweist auf zwei weitere Möglichkeiten im Bereich der Sensorik. Eine davon stellen Optokoppler und Signalverdoppler von WAGO bereit. Sie können ein vorhandenes Ursprungs-Sensorsignal verdoppeln und nutzbar machen. Eine Seite verbleibt in ihrer eigentlichen Funktion, während die andere dann für eine Verdrahtung auf einem IoT Gateway zur Verfügung steht. Im anderen Fall ist die Maschine derart gestaltet, dass sie, qua Maschine „eben tut, was sie tut“. Die Maschine interessiert sich, beispielsweise, in ihrer Funktionalität und als Instanz der Automatisierung nicht für den eigenen Energieverbrauch. Bei der Entwicklung wurde dieser als für sie, in ihrer Funktionalität, nicht relevant erachtet. Daten, die jedoch für eine auswertende Analyse, also aus der Instanz der Digitalisierung heraus gesprochen, Relevanz haben, etwa um einem Produkt oder einer Kostenstelle zugeordnet werden zu können, können dann über eine nachträglich anzubringende Sensorik bspw. zur Messung des Energieverbrauchs abgerufen und nutzbar gemacht werden.
Living on the Edge: Die Flut der Echtzeitdaten
Es sind die Gateways, die Daten aus Maschinen generieren und auf Protokollebene bereitstellen. Mit dem Blick auf die Anforderungen der Zukunft und die damit einhergehende exponentiell anwachsende Zahl von zu verarbeitenden Echtzeitdaten rät Jürgen Pfeifer bei der Skalierung eines großen Maschinenparks immer zur Wahl modularer Hard- und Softwarekomponenten. Ein Gateway sollte sowohl Sensorik, Aktorik als auch die Protokolle zu den Maschinensteuerungen selbst bedienen, lesen und auswerten können. Das garantiert Flexibilität bei wechselnden Anforderungen und neu hinzukommenden Use Cases. Denn je smarter Prozesse werden, desto mehr Rechenleistung wird auch benötigt. Um diese langfristig bereitstellen zu können, sollten Informationen, die die Steuerung einer Maschine nur belasten, direkt auf das IoT-Gateway gelegt werden. Dieses entwickelt sich damit von einem „rein lesenden“ System hin zu einem System, das die Funktion einer Datenbank sowie die Ausführung von Algorithmen zur Analyse und Optimierung direkt im Feld übernehmen kann. Das verkürzt Reaktionszeiten wesentlich, da Daten nicht erst zu einer zentralen Verarbeitung auf einem Server weitergeleitet-, sondern an Ort und Stelle dezentriert verarbeitet werden können. WAGO bietet in dieser Funktion die Produkte „Edge-Controller“ und „Edge Computer“. Die Geräte verarbeiten Anwendungen unmittelbar an der Maschine und entlasten so Steuerungen, die sich auf ihre originäre Steuerungsaufgabe mit geringer Latenz und hoher Deterministik fokussieren können.
WIKA: Messgeräte als Sinnesorgane der Digitalisierung.
Die absolute Schlüsselrolle der Datengewinnung und -analyse hat man auch bei der WIKA Gruppe, ihrerseits führend in Druck- und Temperaturmesstechnik, im Fokus. Auch in den Messgrößen Füllstand, Kraft und Durchfluss sowie in der Kalibriertechnik setzt das Unternehmen Standards. WIKA hat es sich zum Ziel gesetzt, sich im Bereich IIoT bis Mitte des Jahres 2023 zu einem führenden Anbieter ganzheitlicher Kundenlösungen zu etablieren. Geplant sind Applikationen auf einer Cloud Plattform, Konnektivität-Lösungen, der Aufbau eigener Netzwerke als auch IIoT-fähige Messgeräte. Ganz im Einklang mit der eigenen Kernkompetenz „Messtechnik“, betont man hier nämlich vor allem die Rolle der Messdaten, als die Daten, die Aufschluss über den Zustand von Komponenten, Maschinen und Anlagen geben können. Da es immer Messgeräte sind, die diese bereitstellen, sieht man diese als die Grundelemente einer Wertschöpfung durch IIoT an. Doch jeder erste Schritt in der Digitalisierung führt, – auch bei WIKA, erstmal über eine Bestandsaufnahme des Maschinenparks. Erst dann zeigt sich weiter, welche Messdaten digitalisiert werden müssen, – und welche Bestandsgeräte integriert werden können. Um darüber hinaus bestehende Anzeigen IIoT-fähig zu machen, entwickelt WIKA, neben den erforderlichen Digitalsensoren, Manometer mit Wireless-Funktion. Deren Relevanz fasst Alexander Wiegand, CEO, in folgende Worte: „Sensoren sind die Sinnesorgane der Digitalisierung. Spätestens Mitte nächsten Jahres sind wir so weit, dass wir jedes unserer Messgeräte drahtlos mit der Cloud verbinden können.“ Um Konnektivität, bei allen noch so individuell möglichen Ausgangslagen, zu gewährleisten, setzt WIKA auf LPWAN-Standards wie LoRaWAN und MIOTY sowie auf Mobilfunk, nebst Bluetooth und Ethernet. Auch hier verweist man auf die Vorzüge, die eine gelungene umfassende Aufzeichnung, Zusammenführung und Auswertung von Daten mit sich bringt. Sie gestattet die Kontrolle von Normkonformität, also einen reibungslosen Betrieb, mögliche Prozessoptimierung, also die Steigerung von Effektivität bei gleichzeitiger Ressourceneinsparung, bis hin zu Predictive Maintainance. Sie bezeichnet die Möglichkeit einer vorbeugenden Wartung, die von aufgezeichneten Daten sowie von Daten in Echtzeit lernt und entsprechend reagiert. Was man damit erreichen kann, oder auch bereits erreicht hat, wird im nächsten Abschnitt näher beleuchtet.
Voith Group: Mit dem digitalen Zwilling auf dem Weg zur Smart Factory.
Auch bei der Voith Group, einem weltweit agierenden Technologiekonzern mit breitem Portfolio, bestehend aus Anlagen, Produkten, Serviceleistungen und digitalen Anwendungen für die Märkte Energie, Papier, Rohstoffe sowie Transport & Automotive, unterstützt man Industrieunternehmen tatkräftig auf ihrem Weg zur Industrie 4.0. Die „dataPARC cloud“ von Voith bietet ebenfalls zahlreiche Funktionen, um Prozesse und Ressourceneinsatz zu optimieren. Und auch hier bleibt die Verbesserung der betrieblichen Effektivität, Produktivität und Qualität durch intelligente industrielle Systeme und flexible Produktionstechniken natürlich immer ein wichtiger Aspekt. Einen ganz besonderen Schwerpunkt legt Voith jedoch auf weitere Vorteile und Potentiale, die speziell eine ganzheitliche Datenplattform bieten kann: Können alle Anwendungen auf ein- und derselben cloudbasierten technischen Plattform prozessiert werden, ermöglicht die applikations- und standortübergreifende Zusammenführung von Informationen und Daten bislang oftmals ungenutzte Korrelationsmöglichkeiten. Eine verdankt sich einer speziellen Neuerung, die das IIoT hervorgebracht hat, den „Digital Twins“. Im Falle einer ganzheitlichen Datenplattform können diese eine ganze Anlage oder sogar mehrere Fertigungsstandorte virtuell abbilden. Ihr Mehrwert geht weit über die bloße Vernetzung hinaus. Sie erlauben es auch, Betriebsabläufe zu simulieren, wodurch sich zu erwartende Abnutzungserscheinungen und Lebenszyklen, auch von neuen Anwendungen und komplexen mehrstufigen Prozessen, annähernd datieren lassen. Ausfallerscheinungen kommt man somit einfach zuvor, indem man die rechtzeitige Wartung von vornherein anhand einer Prognose mit einplant. Darüber hinaus können verschiedenste Szenarien durchgespielt werden. Auch Innovationen lassen sich erstmal virtuell erproben, allerdings eben ohne dabei ein reales Risiko eingehen – und tatsächliches Kapital aufwenden zu müssen. Eine weitere und entscheidende Möglichkeit besteht in der Miteinbeziehung von externen Datenquellen, wie beispielsweise dem Wetterbericht, aktuellen Rohstoffpreisen, oder auch den Anbindungen an Online-Stores, an Lager und alle weiteren unternehmensübergreifenden Instanzen einer Wertschöpfungskette. Es ist diese offene und übergreifende Struktur, die ein optimal genutztes IIoT ausmacht und mithilfe derer man immer mehr an das Ziel dessen gelangt, was Industrie 4.0 wirklich bedeuten kann.
Die vierte industrielle Revolution: Die virtuelle Steuerung der Realität
Mit den Worten von Voith bedeutet es die Vernetzung von Maschinen, Gegenständen und Assets, die es Fabriken auf der Basis intelligenter Technologien erlaubt, sich selbst zu steuern, sie also zu „Smart Factories“ macht. Das Whitepaper des Fraunhofer Instituts verweist an dieser Stelle auf die Sicht des World Economic Forums, das die prägende Kraft des IIoT auch ausdrücklich als weit über betriebswirtschaftliche Effekte hinausgehend, folgendermaßen beschreibt: „Es wird die globale Tragweite des Internets mit einer neuen Fähigkeit verbinden, nämlich die physikalische Welt direkt zu steuern, einschließlich Maschinen, Fabriken und Infrastruktur, die die moderne Landschaft prägen.“ (…) „Für diese hochvernetzte Produktion – von der Idee über die eigentliche Fertigung bis zu Wartung und Support – wird in Deutschland auch der Terminus Industrie 4.0 gebraucht: […] die vierte industrielle Revolution, einer neuen Stufe der Organisation und Steuerung der gesamten Wertschöpfungskette über den Lebenszyklus von Produkten. Dieser Zyklus orientiert sich an zunehmend individualisierten Kundenwünschen und erstreckt sich von der Idee, dem Auftrag über die Entwicklung und Fertigung, die Auslieferung eines Produkts an den Endkunden bis hin zum Recycling, einschließlich der damit verbundenen Dienstleistungen.“ Bedingung dieser Möglichkeit bleibt eine durch Vernetzung gewährleistete Verfügbarkeit aller wichtigen Informationen, von allen relevanten Instanzen in Echtzeit, sowie die Kenntnis, diese gezielt einzusetzen. Die Verbindung von Menschen, Objekten und Systemen bringt dann dynamische, echtzeitoptimierte, sich selbst organisierende und unternehmensübergreifende Wertschöpfungsnetzwerke hervor, die sich nach unterschiedlichen Kriterien optimieren lassen. Der Startschuss ist in vielen Familienunternehmen bereits gefallen: Willkommen in der Zukunft!
WIKA setzt auf IIoT – und rückt dieses Thema als Ausrichter des „Karrieretages Familienunternehmen“ ebenfalls in den Fokus. Dieser wird in dem neuen Entwicklungszentrum stattfinden. Die größte Investition der Firmengeschichte soll die Weichen für eine weiterhin erfolgreiche Unternehmensentwicklung stellen. Hier sollen die Produkte und Dienstleistungsangebote von Morgen entstehen. Dazu werden engagierte Mitarbeiter:innen benötigt, die über den Tellerrand hinausschauen, zukünftige Anforderungen antizipieren und in innovative Lösungen umsetzen. Hier unterstützt der „Karrieretag Familienunternehmen“, die europaweit erste und einzige Recruiting- und Kontaktmesse speziell für Karrieren in Familienunternehmen und beim „Hidden Champion“. Angesprochen werden Absolvent:innen, Young Professionals und Professionals aller Fachrichtungen, insbesondere Ingenieur:innen, Informatiker:innen und Wirtschaftswissenschaftler:innen.
Jetzt noch per Schnell-Bewerbung bis 11. November 2022 für den 28. Karrieretag Familienunternehmen am 25. November 2022 bei der WIKA Alexander Wiegand SE & Co. KG in Klingenberg am Main bewerben: www.karrieretag-familienunternehmen.de
[1] „Neue Studie zu Industrial IoT: Deutsche Industrieunternehmen haben Potenzial verschlafen“, International Data Cooperation (IDC), Mai 2022
„Karriere im Familienunternehmen“ als Initiative des Entrepreneurs Clubs hat sich zum Ziel gesetzt, Fach- und Führungskräfte über das Karriereumfeld in der Unternehmensklasse der Familienunternehmen aufzuklären. Die Ergebnisse langjähriger wissenschaftlicher Forschung und Praxiserfahrung in der Zusammenarbeit mit großen Familienunternehmen sind Basis eines crossmedialen übergeordneten Marketingkonzepts unter der Dachmarke „Karriere bei Deutschlands führenden Familienunternehmen“.
Der Entrepreneurs Club
Ismaninger Straße 115
81675 München
Telefon: +49 (89) 4161465-0
Telefax: +49 (89) 4161465-99
https://www.entrepreneursclub.eu
Karriere im Familienunternehmen
Telefon: +49 (0)89 4161465-70
E-Mail: presse@entrepreneursclub.eu